
LEATHER
Our leathers come in many different colours and finishes but are all from European tanneries. Leather has been used for centuries to make footwear due to it’s great flexibility and durability. The natural material ensures each upper will have it’s unique character which will develop patina with wear.
WOOD
We use alder and lime wood because of their excellent moisture absorption properties that helps keep your feet comfy and dry. The natural properties of the wood ensures no wooden bottom will look quite the same. There will always be small imperfections and patterns in the wood that makes each pair of clog bottoms unique.
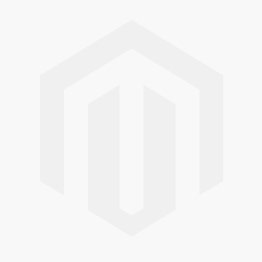
Making

WOODEN BOTTOMS
Working the wood is a long process which starts with sawing logs into planks of different dimensions depending on the shape and size of bottoms that are going to be made. Once this has been done we move the planks into our wood dryer where they stay for several weeks until the correct moisture content is reached. Once dry, our craftsmen start working the wood through different milling operations, attaching soles and finally polishing the instep and sides until a beautiful Maguba bottom is ready to become a clog. Before nailing the clogs, the wooden bottoms are died into brown or black and/or varnished as necessary.
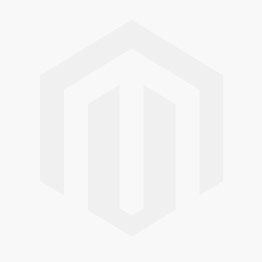
LEATHER UPPERS
Our clickers first carefully inspects the hides for imperfections and then determines which direction to cut the leather. Once this has been done they proceed to cut our clog uppers. The different pattern pieces are then stitched together and buckles and eyelets are attached on the styles where this is required.
Both clicking and sewing are crafts that take years to learn properly.
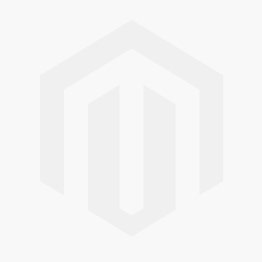
NAILING & LASTING
The clog cobbler carefully nails the upper onto the wood. The craftsmen and women doing the nailing must take into consideration the style of the upper and the shape of the bottoms to ensure a good fit on the last.
Depending on the clog style, the upper will be lasted before or after we nail them onto the wood. Before lasting, the leather uppers are conditioned to make them flexible and ready to take on the shape of the last. Once lasted the uppers are checked again before entering the drying room. Once dry the clogs are put to cool down before the last are removed. Proper lasting ensures the clogs keep their shape.